Schaeffler Conducted 3D Scans on 48 of Its Facilities, Resulting in a Substantial 80% Increase in Efficiency.
For corporations like the Schaeffler Group, located primarily in Germany with around 90 factories worldwide, including 10 in the USA, optimizing the production of intricate industrial components is of utmost importance. Starting in 2016, their transition into digitizing operations yielded more real-time data from the workfloor. However, Schaeffler recognized that this digitization of manufacturing processes, inventory, workforce, and logistics wasn't enough. They needed to digitize the physical manufacturing environment itself.
By implementing 3D scanning techniques on each facility, Schaeffler has managed to create highly detailed digital replicas, or digital twins, of their factories. This process has resulted in substantial time and cost savings, with project lead times for data capture being up to 80% shorter compared to traditional methods. According to Roberto Henkel, Schaeffler's senior VP of digitalization and operations IT, these digital replicas have substantially improved communication and planning across departments and third-party vendors.
As Schaeffler expedites factory relocations to minimize supply chains and manufacture closer to customers, precise digital twins have proven invaluable and provided unexpected advantages.
Creating an accurate digital twin of an entire physical factory is no easy feat.
Progress in Location Reality Capture
Today's virtual environments, such as property virtual tours or Google Street Views, are typically composed of multiple photographs stitched together using software algorithms that identify areas of overlap. Although this method can generate a 3D environment suitable for visual representations, it's lacking in the precision and speed required for a functioning digital twin of a factory. For this, companies tend to rely on laser 3D scanning, specifically LiDAR (light detection and ranging) coupled with high-resolution imagery and simultaneous localization and mapping (SLAM) technology, which enables real-time mapping of indoor spaces, even in GPS-devoid environments.
Though this technology has existed for years, traditional tripod-mounted scanners can take between several months to a year to digitally scan an engine factory. The advent of newer, wearable mobile laser scanning technology has allowed data to be captured at walking speed, thanks to cloud-based processing and sophisticated algorithms.
One pioneering German company, NavVis, developed a wearable 3D scanner, the NavVis VLX, and a digital twin platform called NavVis Ivion for capturing and rendering indoor environments in 360°. NavVis' technology is widely used across industries, including construction, manufacturing, and real estate, to generate high-resolution digital models of complex indoor spaces.
Schaeffler adopted NavVis' technology in 2020 and now scans factories in less than a week, having scanned more than 16 million square feet to develop digital twins for 48 facilities.
Highly accurate, full-color digital twins enable Henkel and his team to address a multitude of concerns often encountered during relocation projects. As Schaeffler continually optimizes its production footprint by moving product lines and value streams between locations, details like equipment status, required changes at the new location, and tools are vital to ensure seamless transitions.
NavVis' wearable 3D scanner, or mobile mapping device, captures data on the factory environment and all of its equipment down to every door knob and light switch. NavVis also offers a reality capture service for companies just starting their digital capture journey.
Though handheld 3D scanners from Leica, Faro, and Kaarta utilize LiDAR and SLAM technology, they are not wearable. Solutions from scanner manufacturers Faro and Trimble require a tripod base. Another limited wearable 360° scanning technology, California-based GreenValley International's LiBackpack, is primarily designed for outdoor environments, such as forests, construction sites, and large-scale land surveying.
However, scanning is only part of the solution; data interpretation and manipulation are also crucial. NavVis Ivion enables users to tag and annotate environments, log equipment placement, and precisely measure spaces, facilitating seamless integration into new factory plans.
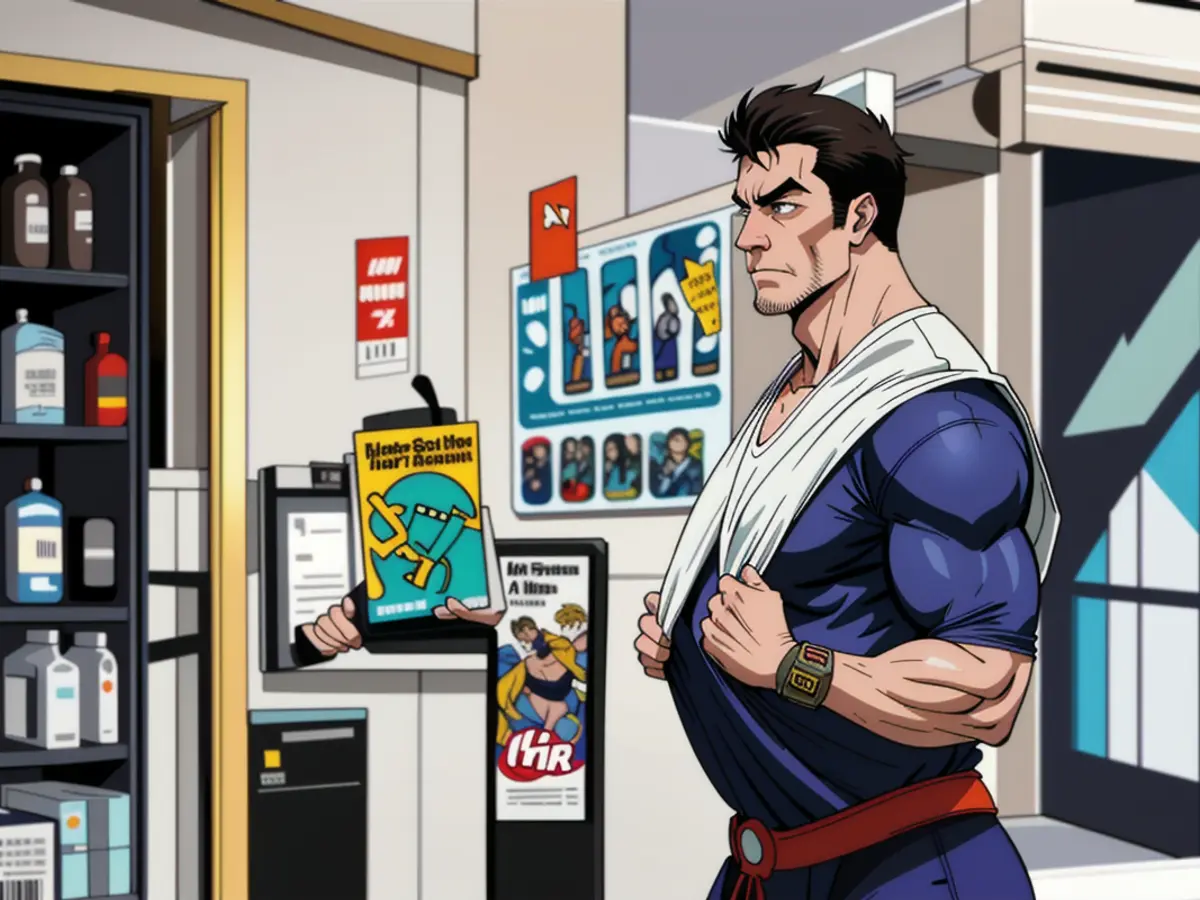
After scanning a few factories, Henkel discovered new applications and insights from the data, inspiring departments beyond factory planning, such as maintenance and third-party vendors, to use the platform. Access to the platform makes it easy for these workers to visually explore factory spaces and determine where they need to intervene without committing to frequent site visits.
Schaeffler can seamlessly integrate data from its other IT platforms and manufacturing execution system (MES) to develop virtual shop floor management. "We are working on cases where we can bring in live data from our MES for first shop floor rounds or for discussing potential bottlenecks in machines," says Henkel. "Once we opened the platform to a broader range of different roles, it was quite impressive to see how many innovative ideas emerged for various users."
For Schaeffler's worldwide factories, the primary goal is to centralize and merge more operations into a single facility located near the customer. This move aims to decrease shipping, logistics, storage, and CO2 emissions.
According to Henkel, relocation is a significant area of focus. Components are manufactured in one plant, then shipped to another for additional functionality, followed by transportation to a third and fourth plant. This international shipping process is not only problematic from an environmental standpoint but also adds to the cost.
Schaeffler's factory digital twins aid in identifying opportunities to expand production areas by a few square meters in an existing plant or to identify underutilized facilities.
As Henkel explains, "This feature allows us to make quicker decisions and create more decision-making possibilities."
The Future of Scanning: AI-Powered Digital Twins
Schaeffler and NavVis share ambitions to enhance factory digital twins through partnerships in product development.
Henkel describes a potential scenario, "If you integrate the digital twin with AI, it could recognize and connect real-world assets in scans to our 3D factory planning."
Furthermore, an interactive digital twin that simulates real-time factory processes is a future possibility, yet the technology is not yet fully developed.
Henkel states, "This is our current focus, not only with NavVis, but also with partners like Nvidia, as it requires a host of specialized and highly innovative technologies."
"We see ourselves as leaders in this field, driving innovation within the context of the industrial Metaverse," concludes Henkel.
Following their implementation of 3D scanning techniques, the Schaeffler Group, in collaboration with NavVis, has begun creating digital twins of their factories using LiDAR technology and wearable mobile scanners. This has allowed them to scan factories in less than a week, significantly reducing project lead times.
Furthermore, Schaeffler is exploring the integration of AI with their digital twins, aiming to recognize and connect real-world assets in scans to their 3D factory planning, as suggested by Roberto Henkel, Schaeffler's senior VP of digitalization and operations IT.